7 Tips to Improve Efficiency in Your Cider Bottling and Packaging Line
Improving efficiency in your cider bottling and packaging line is a multi-faceted effort—from floor organization and equipment investment to staff training and sustainable practices.
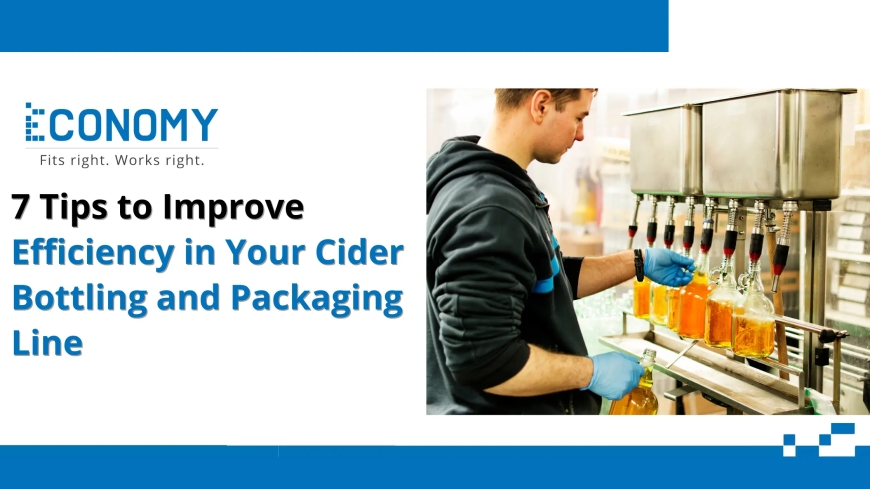
Why Efficiency Matters in Cider Packaging
In the competitive cider market, bottling and packaging efficiency isn't just about speed—it's about quality, cost control, and consistency. An efficient line ensures that your product reaches customers in perfect condition, reduces waste, and minimizes labor and energy costs. From small craft cider makers to large-scale producers, streamlining this final step in production can significantly enhance profitability and brand reputation.
1. Organizing Your Production Floor for Maximum Efficiency
A well-organized floor is the foundation of a smooth-running packaging line. Designate clear zones for each stage—cleaning, filling, capping, labeling, and boxing. Ensure that pathways are clear to reduce unnecessary movement and avoid safety hazards. Tools and materials should be within arm’s reach of each station. Color-coded floor markings and labels for storage areas can enhance workflow visibility and reduce errors.
2. Reducing Bottlenecks in the Workflow
Bottlenecks slow down production, cause downtime, and increase stress for staff. Identify the slowest step in your process and investigate why it’s underperforming—are machines outdated, operators undertrained, or processes too manual? Use production data or observe line activity to pinpoint these issues. Sometimes, simple adjustments like reassigning tasks or tweaking the timing between machines can have a major impact.
3. Optimizing Equipment Placement
The physical layout of your equipment directly affects output. Machines should be arranged in a logical sequence that minimizes handling and movement. Align conveyor systems to prevent crossovers and backtracking. Position your bottling station near the cider storage tank to reduce transfer time. The goal is a continuous, linear flow from start to finish with minimal disruption.
4. Investing in Durable Bottling and Packaging Systems
Cutting corners on machinery might save upfront costs but can lead to higher maintenance, frequent breakdowns, and lost production time. Investing in durable, high-quality bottling and packaging systems ensures longevity, efficiency, and consistent performance. Look for machines with automation capabilities, stainless steel construction, and compatibility with your bottle types and production volume.
Benefits of Reliable Machinery
-
Reduced downtime due to fewer malfunctions
-
Improved product consistency in fill levels and sealing
-
Lower maintenance costs over time
-
Faster changeover times for different bottle sizes or batches
5. Choosing the Right Bottles, Caps, and Labels
Efficiency isn’t just about machinery—it also depends on using compatible, easy-to-handle packaging materials. Bottles should fit seamlessly with your fillers and cappers; using oddly-shaped or non-standard bottles can slow the line. Choose caps that don’t jam the capping heads and labels that feed smoothly into labeling machines. Bulk purchasing compatible materials also helps reduce supply chain disruptions.
6. Preventative Maintenance to Avoid Downtime
Unexpected breakdowns are the enemy of efficiency. Establish a preventive maintenance schedule to regularly inspect, clean, and lubricate your equipment. Include routine tasks like checking belt tension, cleaning nozzles, inspecting capping heads, and verifying label alignment.
Key Components to Inspect Regularly:
-
Fill nozzles and hoses
-
Cap feeding mechanisms
-
Conveyor belts and motors
-
Label application rollers
Signs of Wear and Tear to Address:
-
Inconsistent fill levels
-
Misaligned or loose caps
-
Slipping conveyor belts
-
Machine vibrations or strange noises
By addressing minor issues before they become major failures, you can maintain a smoother and more reliable bottling line.
7. Enhancing Efficiency with Modern Tools
Modern technology offers several ways to boost productivity and reduce human error.
Automated Bottle Filling Machines
Automated fillers offer precise control over fill levels, reduce product loss, and speed up production. Look for options with programmable controls to adjust for different batch sizes or product viscosities.
Monitoring Systems for Real-Time Data
Implement real-time monitoring systems to track key performance indicators (KPIs) like output rate, machine uptime, and rejection rates. These insights help operators respond quickly to issues and support continuous improvement efforts.
Sustainable Practices for Bottling and Packaging
Sustainability and efficiency often go hand in hand. Reducing waste saves money and aligns with consumer demand for environmentally responsible products.
Minimizing Spillage During Bottling
Install anti-drip nozzles or vacuum-assisted filling to reduce product spillage. Not only does this preserve more cider per batch, but it also keeps the line cleaner and reduces downtime for cleaning.
Recycling Packaging Materials
Use recyclable bottles, caps, and cartons where possible. Establish a system for collecting and recycling damaged packaging during the bottling process. Consider sourcing from suppliers who offer sustainable options.
Maximizing Productivity in Your Cider Bottling Line
Improving cider bottling line efficiency and packaging line is a multi-faceted effort—from floor organization and equipment investment to staff training and sustainable practices. Each adjustment contributes to smoother operations, lower costs, and a better-quality product. When your line runs efficiently, you not only bottle more cider—you build a better business.