Digitizing Design Control: Strategies for Modernizing Medical Device Product Lifecycle
Explore how digitizing design control for medical devices enhances regulatory compliance, accelerates innovation, and improves product quality. Learn how digital systems streamline collaboration, risk management, and traceability, ensuring faster time-to-market while maintaining safety and compliance.
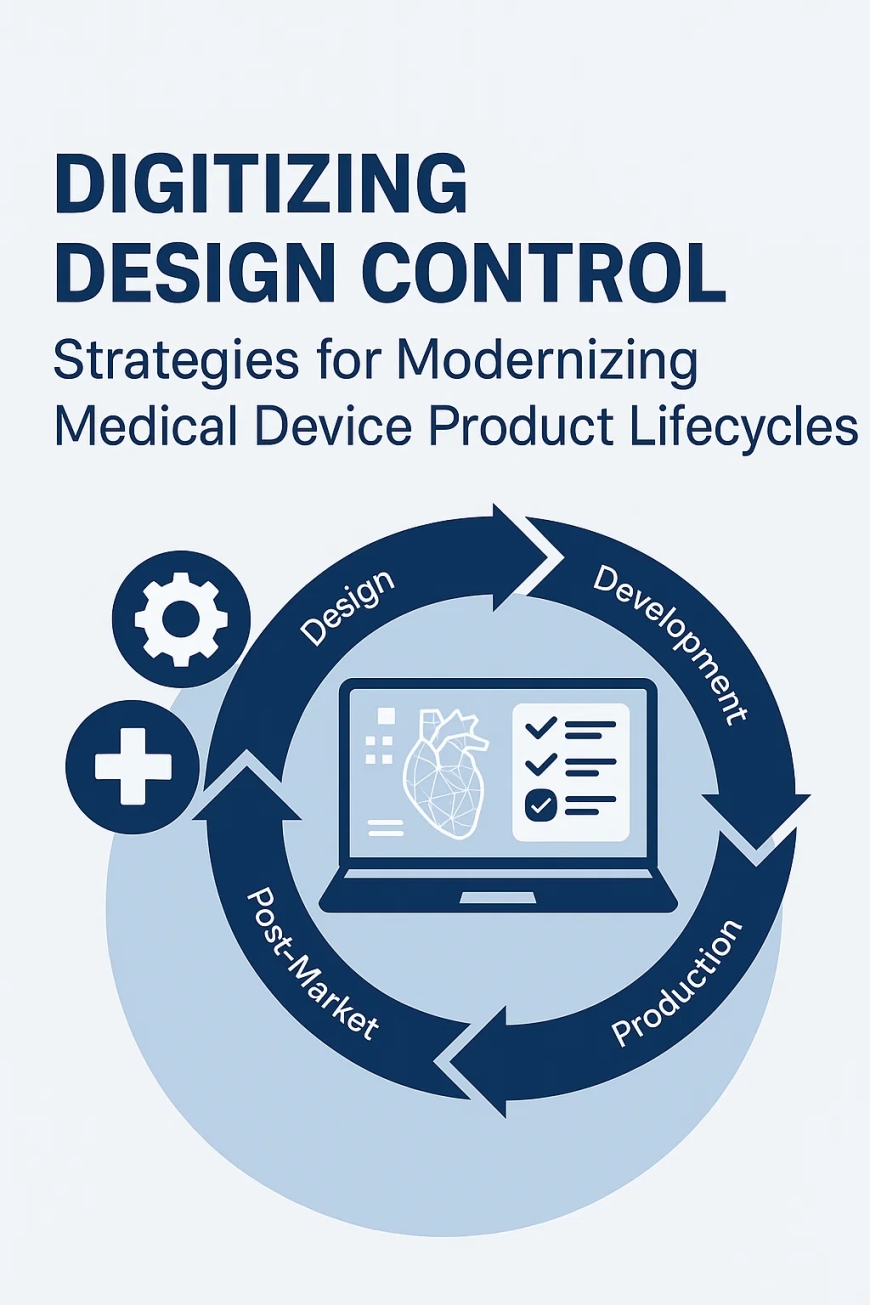
Evolving the Role of Design Control for Medical Devices in the Digital Era
The medical device industry is under unprecedented pressure to accelerate innovation while maintaining stringent regulatory compliance. This dual imperative makes Design Control for Medical Devices a cornerstone of successful product development. As regulatory expectations become more complex and globalized, digitization emerges as the critical enabler of speed, traceability, and compliance.
Today, organizations that digitize design control medical device processes are positioned to enhance collaboration, improve product quality, and streamline submissions to agencies like the FDA. Implementing a robust digital approach to medical device design controls ensures a closed-loop system that enhances both quality and safety throughout the product lifecycle.
Building a Connected Digital Framework for Design Control for Medical Devices
To fully leverage the potential of digitization, medical device companies must establish a centralized digital ecosystem. At the core of this framework is a purpose-built solution that connects design inputs, outputs, verifications, validations, and design reviews.
By creating a single source of truth for design control for medical devices, organizations can ensure full traceability and reduce the risk of disconnected processes. Integrating this system with Quality Management Software allows real-time tracking of changes and provides complete visibility into compliance gaps.
Driving Regulatory Alignment Through Digital Medical Device Design Controls
Achieving regulatory alignment, particularly with the FDA's 21 CFR Part 820 and ISO 13485:2016, requires meticulous attention to detail. Digital systems supporting design control medical device processes enable automatic linking of user needs to design outputs and verification steps.
Through structured workflows and automated documentation, organizations minimize manual errors and prepare audit-ready records. Such proactive regulatory alignment demonstrates a strong commitment to quality and safety, ultimately facilitating faster product approvals.
Accelerating Innovation Without Compromising Compliance
Traditionally, ensuring compliance with medical device design controls often meant delaying innovation to accommodate rigorous documentation cycles. Digitized systems break this trade-off by streamlining documentation, approvals, and review cycles, thereby accelerating time-to-market.
Automated alerts, review schedules, and digital signatures ensure that all aspects of the product development lifecycle are continuously monitored and compliant. This modernized approach supports agile development methodologies while adhering to regulatory mandates.
Integrating Risk Management into Digital Design Control for Medical Devices
Risk management is intrinsically tied to design control for medical devices. A modern approach integrates risk management activities such as hazard analysis, risk control measures, and failure mode analysis directly within the Design Control process.
Digitization allows companies to assess risk in real time, automatically update risk files as design changes occur, and provide regulators with comprehensive risk traceability matrices. This seamless integration enhances product safety and demonstrates an organizational culture focused on continuous improvement and compliance.
Improving Cross-Functional Collaboration Across Global Teams
Effective design control medical device strategies rely on tight collaboration between R&D, quality, manufacturing, and regulatory teams. A digital system enables cross-functional teams to work within a shared environment, facilitating instant access to updated files and design histories.
This collaboration eliminates delays caused by email chains or disjointed data repositories. The result is improved decision-making, reduced rework, and consistent compliance across every phase of the product lifecycle.
Leveraging Analytics to Improve Outcomes in Medical Device Design Controls
Analytics play a transformative role in optimizing design control for medical devices. By analyzing trends in non-conformances, approval timelines, and verification failures, companies can proactively address systemic issues and drive design excellence.
A digital Quality Management Software platform provides dashboards and KPIs that offer insight into process health. This enables decision-makers to make data-driven choices that directly impact the speed, quality, and compliance of medical device development.
Enhancing Document Control to Support Medical Device Design Controls
Document management is integral to the design control process. Digitized document control systems help manage controlled documents like design inputs, test protocols, validation plans, and DHF (Design History File) records.
By integrating document control with broader design control for medical devices processes, organizations reduce duplication, enforce version control, and ensure accessibility for auditors. This structure supports efficient audits and regulatory submissions, reducing delays and inconsistencies.
Ensuring Seamless Traceability Across the Medical Device Product Lifecycle
One of the most challenging aspects of regulatory compliance is maintaining full traceability from user needs through to design validation. Digitized design control medical device systems support traceability matrices that are automatically updated and always inspection-ready.
Whether tracking changes to user requirements or linking test results to Risk Mitigations, digital traceability ensures end-to-end visibility. This capability is crucial for demonstrating conformance during FDA inspections or ISO audits.
Aligning Product Lifecycle Management with Design Control Objectives
Modern PLM strategies rely heavily on integrated digital environments where design control for medical devices plays a pivotal role. Linking PLM and QMS systems enables consistent documentation, faster design freeze, and early detection of issues across the product lifecycle.
This alignment ensures that design decisions are informed by real-world performance data, post-market surveillance, and supplier feedback. It creates a learning loop that drives continuous improvement and lifecycle sustainability.
Conclusion: Why ComplianceQuest is Essential for Business in 2025
In 2025 and beyond, the medical device industry will face even greater regulatory scrutiny, innovation pressure, and operational complexity. To remain competitive, organizations must prioritize digitization—particularly in areas like design control for medical devices. ComplianceQuest offers a cloud-native, highly scalable platform that transforms the way companies manage product development and regulatory compliance.
By digitizing medical device design controls and integrating with risk, document, and quality systems, ComplianceQuest provides a unified environment that enhances quality and safety while reducing time-to-market. With built-in analytics, robust workflows, and seamless traceability, it empowers regulatory, quality, and R&D leaders to operate with confidence.
Choosing ComplianceQuest is not just a technological decision—it's a strategic move toward excellence, global market readiness, and sustained growth.