Flight Validation with CTS: Testing Without Release
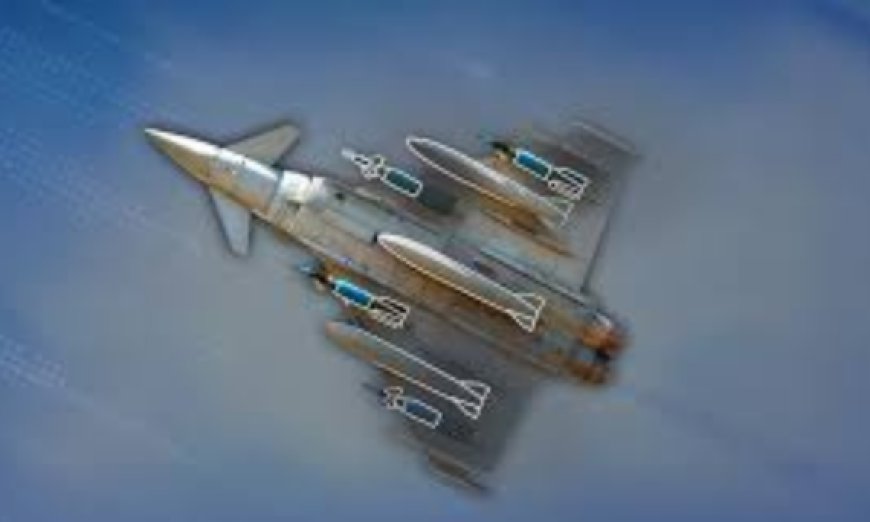
In modern aerospace and defense industries, where safety and accuracy are paramount, extensive testing is mandatory before any weapon system becomes operational. One such critical phase is CTS Testing, or Captive Trajectory System Testing. This method allows engineers to evaluate the behavior of air-launched weapons and pods—without releasing them—while collecting real-time data on their interaction with the host aircraft.
What Is CTS Testing?
CTS Testing refers to a series of in-flight tests where a weapon or store is mounted on an aircraft in a captive (non-droppable) state. The purpose is to monitor its aerodynamic and structural behavior during different phases of flight, before any actual release takes place.
It’s often one of the first in-flight tests performed after a store has been mounted, serving as a bridge between ground testing and live-fire trials.
Why Use CTS Testing?
When integrating a new missile, bomb, or external pod onto an aircraft, it’s not enough to check mechanical compatibility. Engineers must assess how the store interacts with airflow, structural vibrations, and avionics systems—before committing to a live release.
CTS Testing offers the following advantages:
-
Safety: Reduces risk by preventing premature or unstable release.
-
Validation: Confirms if the store behaves as predicted in computational simulations.
-
Cost Efficiency: Helps detect design flaws early, avoiding costly release test failures.
-
System Integration: Ensures proper functioning of electrical interfaces, targeting systems, and power supply.
-
Certification Support: Provides crucial data for regulatory and defense agency certification.
Key Objectives of CTS Testing
CTS Testing is not just about flying with the store attached—it serves a series of technical objectives:
-
Evaluate Store Behavior in Flight
-
Aerodynamic stability
-
Vibrations and oscillations
-
Store-induced structural loads
-
-
Test Store-Aircraft Integration
-
Mounting and pylon performance
-
Electrical and data connectivity
-
Environmental effects on store electronics
-
-
Validate Predictive Models
-
Compare actual data with CFD (Computational Fluid Dynamics) simulations
-
Improve accuracy for future release trajectory predictions
-
-
Prepare for Live Release
-
Identify any risks that must be addressed before moving on to separation and release testing
-
Phases of CTS Testing
CTS Testing is often performed in stages to gradually increase risk and complexity:
1. Initial Captive Carry
-
The store is unpowered and inert.
-
Focuses on aerodynamic drag, vibration, and mounting integrity.
-
Helps confirm basic flight safety with the store attached.
2. Captive Carry with Instrumentation
-
The store is outfitted with sensors and telemetry.
-
Engineers measure real-time structural loads, vibrations, pressure distribution, and electronic behavior.
3. Captive Carry with Power-On Systems
-
Activates the weapon’s internal electronics (such as seekers, guidance systems, or RF links) during flight.
-
Simulates operational mission profiles without releasing the store.
Core Components of a CTS Test Setup
CTS Testing involves multiple integrated systems working together:
● Instrumented Store or Pod
Equipped with sensors such as:
-
Strain gauges
-
Accelerometers
-
Pressure sensors
-
Gyroscopes
-
GPS and IMUs
● Aircraft Flight Test Instrumentation (FTI)
-
Collects and transmits data from the store to ground control.
-
Includes telemetry systems, data loggers, and onboard control units.
● Ground Telemetry and Control Station
-
Receives live data during the flight.
-
Allows test engineers to monitor performance and abort if anomalies are detected.
Test Execution Process
CTS Testing follows a structured and highly coordinated process:
1. Test Planning
-
Define test objectives, flight conditions, and safety measures.
-
Simulate store behavior with CFD and wind tunnel data.
2. Ground Integration
-
Mount store and connect electronic systems.
-
Validate power, data, and safety interlocks.
3. Flight Test
-
Fly the aircraft through defined maneuvers (e.g., level flight, dives, turns).
-
Record and transmit all sensor and system data in real time.
4. Post-Flight Analysis
-
Engineers evaluate aerodynamic and structural data.
-
Identify any unexpected loads, resonance, or interference.
Data Collected During CTS Testing
CTS Testing provides valuable data, including:
-
Load profiles: Forces acting on pylons and mounts
-
Vibration signatures: Detect resonance or fatigue risk
-
Pressure readings: Aerodynamic behavior at various altitudes
-
Thermal data: Store surface and internal component temperatures
-
System health: Store avionics and power performance
Common Applications of CTS Testing
CTS Testing is used in various military and aerospace programs, especially in:
-
Missile integration (e.g., air-to-air or air-to-ground systems)
-
Smart bomb carriage testing
-
Electronic warfare pods and countermeasure systems
-
Reconnaissance pods
-
Fuel tanks and drop tanks
-
UAV payload testing
Challenges in CTS Testing
While CTS is a critical tool, it comes with challenges:
-
Sensor reliability: Faulty sensors can lead to misleading data.
-
Aircraft modification: Requires complex wiring and mounting for each store.
-
Flight test constraints: Weather, airspace, and scheduling affect timelines.
-
Data overload: Handling and analyzing large volumes of data requires advanced tools and experienced analysts.
Real-World Example
Imagine a new air-to-ground missile is being integrated onto a strike aircraft. Before the first live-fire test:
-
CTS Phase 1: The missile is mounted inert. Engineers evaluate drag and vibration.
-
CTS Phase 2: Missile sensors and avionics are powered on. Data is gathered in real-time.
-
CTS Phase 3: A full mission profile is flown, simulating targeting and lock-on, with the store remaining captive.
-
Data Evaluation: Engineers determine whether the missile behaves safely and predictably, before authorizing release testing.
The Future of CTS Testing
The next generation of CTS Testing will benefit from:
-
AI and ML for Data Analysis: Automated identification of performance issues or structural risks.
-
Digital Twin Integration: Real-time syncing of test data with 3D models for simulation refinement.
-
Smaller, Smarter Sensors: Improved accuracy with minimal weight or space impact.
-
Wireless Telemetry: Cleaner and more flexible aircraft/store integration.