Mastering Weapon Safety with Captive Flight Testing
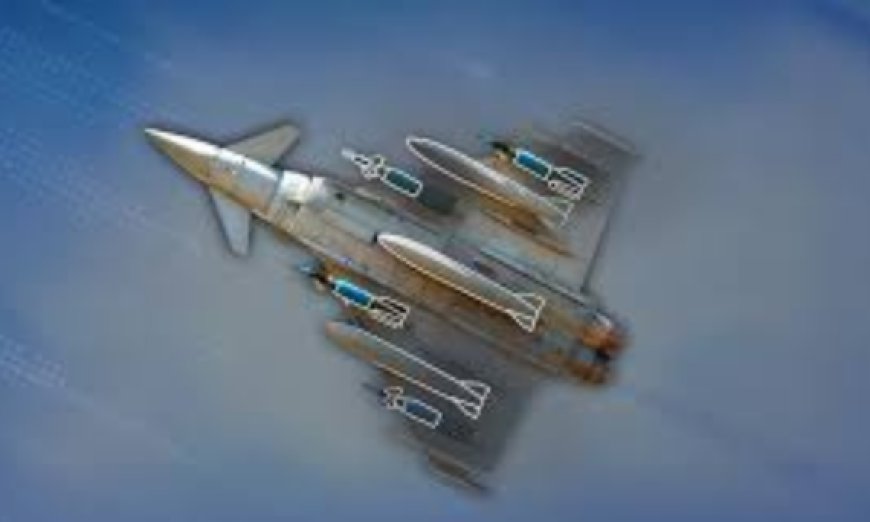
In the high-stakes world of military aviation, where precision and safety are paramount, every new weapon system undergoes extensive testing before it becomes operational. One of the most vital stages in this process is Captive Trajectory System (CTS) Testing.
This specialized form of testing allows defense engineers to evaluate how a weapon or store (like a missile or bomb) behaves when carried by an aircraft—without actually releasing it. It’s a critical step that bridges the gap between ground testing and live-fire trials.
What Is Captive Trajectory System Testing?
Captive Trajectory System (CTS) Testing is an in-flight testing process in which a store (typically a missile, smart bomb, or external pod) is carried on an aircraft in a non-releasable, captive state. The store remains attached to the aircraft during the entire flight, while engineers monitor its behavior through embedded sensors and telemetry systems.
Unlike live release or separation tests, CTS testing focuses on collecting performance data without detachment. This allows engineers to safely analyze store behavior under real flight conditions, which helps refine both system design and mission planning.
Why Is CTS Testing Important?
Releasing a store from an aircraft involves complex dynamics: airflow around the aircraft, vibration, structural loads, separation trajectory, and weapon system activation. If these dynamics are not properly understood and controlled, they could lead to:
-
Unstable or unsafe release
-
Collision with the host aircraft
-
Failure of the weapon’s guidance system
-
Structural damage to the pylon or mount
-
Inaccurate targeting
CTS Testing helps prevent such failures by offering critical insight into how the weapon and aircraft interact before live deployment begins.
Primary Objectives of CTS Testing
CTS Testing is designed to achieve several key goals:
-
Assess Aerodynamic Behavior
Determine how the store interacts with the aircraft and airflow under various flight conditions (speed, altitude, G-forces). -
Monitor Structural Loads
Capture stresses, strains, and vibrations on the store and mounting hardware. -
Validate Simulation Models
Use real flight data to improve the accuracy of Computational Fluid Dynamics (CFD) and structural models. -
Test System Integration
Ensure that onboard electronics, guidance systems, and aircraft interfaces are operating properly under realistic flight profiles. -
Prepare for Live Release Testing
Identify and correct potential hazards before actual weapon deployment occurs.
When Is CTS Testing Used?
CTS Testing is commonly applied in:
-
New missile development programs
-
Integration of existing weapons onto new aircraft
-
Certification of electronic warfare pods and external fuel tanks
-
Testing smart bombs and guided munitions
-
UAV payload integration
Essentially, any system that will eventually be released from an aircraft undergoes CTS testing first.
Types of Captive Testing Flights
CTS Testing is usually divided into phases, depending on the complexity of the system being tested:
1. Captive Carry Flight
-
The store is unpowered and inert.
-
Used to evaluate the aerodynamic and structural effects of carrying the store.
2. Captive Flight Test (CFT) with Instrumentation
-
The store is equipped with telemetry, sensors, and sometimes power systems.
-
Engineers collect high-resolution flight data.
3. Power-On Captive Testing
-
The store’s internal electronics (guidance, sensors, or seekers) are powered and functional.
-
This phase simulates a real mission, short of actual weapon release.
Key Components of a CTS Test Setup
To perform CTS Testing, a combination of specialized systems and tools is required:
● Instrumented Store
Fitted with:
-
Strain gauges
-
Accelerometers
-
Pressure sensors
-
Gyroscopes
-
Thermal sensors
These devices measure how the store responds to various flight conditions.
● Telemetry System
-
Transmits real-time data to ground control during flight.
-
Allows live monitoring and emergency response if needed.
● Data Acquisition System (DAS)
-
Collects and logs thousands of data points per second from the store.
-
Supports post-flight analysis and comparison with simulation results.
● Ground Control Station
-
Engineers monitor live data and control onboard systems during the flight.
-
Also responsible for safety aborts if anomalies occur.
CTS Testing Workflow
A typical CTS testing campaign follows these steps:
1. Test Planning
-
Define objectives, test conditions, safety parameters, and instrumentation layout.
-
Build predictive models using wind tunnel data and CFD.
2. Ground Integration
-
Mount the store to the aircraft’s pylon or carriage system.
-
Connect all sensors, power supplies, and data lines.
3. Pre-Flight Checks
-
Power-up systems, test connectivity, and verify sensor functionality.
4. Captive Flight Execution
-
Fly the aircraft through a predefined set of flight profiles: level flight, turns, dives, and climbs.
-
Record all flight parameters and system responses.
5. Post-Flight Analysis
-
Compare real data with simulation predictions.
-
Identify any anomalies or issues that need to be corrected before live firing.
Benefits of Captive Trajectory System Testing
-
✅ Safety First: Eliminates the risk of an unstable or premature release.
-
✅ Accurate Data Collection: Provides valuable real-world data for improving models and designs.
-
✅ Cost-Efficient: Detects and corrects problems early in the process.
-
✅ Supports Certification: Required for military and regulatory approvals.
-
✅ Flexible Testing: Can be conducted with both manned aircraft and UAVs.
Common Challenges in CTS Testing
Despite its benefits, CTS testing is not without difficulties:
-
High Cost of Instrumentation: Sensors and data systems are expensive and require careful calibration.
-
Aircraft Availability: Test flights need specially instrumented aircraft and crews.
-
Data Complexity: Processing large amounts of sensor data requires advanced software and expertise.
-
Test Environment Limitations: Weather, airspace restrictions, and mission planning can cause delays.
Real-World Example: Missile Integration on a Fighter Jet
Let’s say a new medium-range air-to-air missile is being tested for integration with a multi-role fighter aircraft. The steps might include:
-
Mounting the missile (with sensors) on a wing pylon.
-
Running ground-based vibration and electronic interface tests.
-
Flying the aircraft with the missile through a series of maneuvers.
-
Capturing real-time data on loads, vibrations, seeker performance, and airflow interaction.
-
Analyzing the results to confirm that the store can be safely released in the next phase.
The Future of CTS Testing
With the evolution of digital technology, CTS Testing is also advancing:
-
AI-Powered Data Analysis: Helps detect potential issues faster.
-
Digital Twins: Real-time virtual models of store-aircraft interaction allow for more predictive testing.
-
Wireless Telemetry: Simplifies setup and reduces aircraft modifications.
-
Modular Sensor Systems: Quicker reconfiguration between tests saves time and cost.